Resumen
El trabajo fue realizado en la Empresa DURALMET. El objetivo principal del trabajo fue elaborar un plan de mejoras de diseño y de la operación del horno de secado de pintura de la Empresa de DURALMET, por sus altos consumos energéticos debido a problemas de diseño y operación del mismo.
Se realizó un diagnóstico del horno, incluyendo su ciclo de trabajo, y se cuantificaron las pérdidas de energías. Se realizaron dos estudios: estudio de la calidad del secado de pintura, a diferentes regímenes de temperatura y tiempo, obteniéndose una ecuación de dependencia con el objetivo de poder variar estos parámetros sin afectar la calidad. El segundo estudio se enmarcó en la disminución de las pérdidas de energía y en la recuperación del calor de los productos al salir del horno, proponiéndose mejoras. Con el trabajo se plantea que es posible disminuir cerca del 50% del actual consumo.
Palabras claves: Horno eléctrico, secado de pintura en polvo, transferencia de calor, absorción del calor.
SUMMARY
The study was conducted at the production company DURALMET. The main objective of this study was to develop an improvement plan design and operation of the drying oven paint DURALMET Company, for their high energy consumption due to poor design and operation of the energy consumption.
A diagnosis of the oven, including duty cycle, and quantified the energy losses. We conducted two studies: consideration of quality paint drying at different temperature regimes and time, obtaining an equation of dependence in order to vary these parameters without compromising quality. The second study was framed in reducing power losses and heat recovery products out of the oven, proposing improvements.
With the paper argues that it is possible to reduce about 50% of current consumption.
Keywords: electric oven, drying powder, heat transfer, heat absorption.
INTRODUCCIÓN
El Desarrollo Energético de la sociedad está basado en el uso de los combustibles fósiles principalmente, y en menor medida, en dependencia del nivel de desarrollo y disponibilidad de recursos naturales, se encuentra la energía nuclear y el agua(Turrini 2006). A raíz de la actual crisis energética mundial, se trazó una nueva estrategia en nuestro país llamada Revolución Energética. Esta política energética considera, entre otros, los siguientes aspectos:
- Uso racional de la energía, con el máximo ahorro en su uso final y la utilización de tecnologías de alta eficiencia.
- Desarrollo de tecnologías para el uso generalizado de las fuentes renovables de energía, con un peso progresivo en el balance energético nacional.
En la práctica industrial, uno de los mayores consumidores de energía lo constituyen las operaciones desarrolladas en los hornos, empleados con diferentes fines acorde a las funciones que realiza en una empresa o fábrica determinada, desde la fundición de metales, cocción y vidriado de cerámicas, el tratamiento térmico y el recubrimiento de superficie. En esta última se encuentran los utilizados en el proceso de pintado en superficies metálicas con pintura en polvo, tecnología utilizada en la empresa DURALMET de Las Tunas.
Esta empresa ofrece productos competitivos como Carpintería Galvanizada, pintado de aluminio y prestación de Servicios de Posventas con Calidad para satisfacer las necesidades del cliente. Este proceso incluye en su flujo productivo la utilización de un horno.
En el diagnóstico realizado al horno de secado de pintura en polvo se pudo determinar lo siguiente:
- Los productos y sus soportes salen a altas temperaturas, y este calor no se recupera.
- Existe gran fluctuación de la temperatura en el interior del horno, no permaneciendo a las temperaturas recomendadas por le fabricante.
- Paredes del horno mal o no aisladas térmicamente.
- La calidad del producto es buena.
Los aspectos antes señalados influyen directamente en los consumos de portadores energéticos (Alegría Felices 1982; Molina Igartua 1993), por lo que se debe trabajar en alcanzar rangos eficientes en el consumo energético.
El objetivo principal de la investigación fue elaborar un plan de mejoras de diseño y de la operación del horno de secado de pintura en polvo de la Empresa de DURALMET, para disminuir su consumo energético, sin afectar los parámetros de calidad.
MÉTODOS Y MATERIALES EMPLEADOS
Balance energético del horno
El horno a estudiar es del tipo eléctrico por resistencia eléctrica, con dos baterías de resistencia eléctrica, con un consumo de 36 kWh, estas intercambian calor con aire tirado de manera forzada por dos ventiladores centrífugos. La regulación de su temperatura es a partir de un sistema automático que presenta un termopar entre otros dispositivos, situados en un lado del horno. La operación del horno es periódica con ciclos de horneado de
minutos, y en cada jornada trabaja en promedio
horas. Para la realización del balance térmico en el horno, se define el sistema a trabajar reflejado en la figura 1. Los flujos de energías se analizan en los epígrafes posteriores.
Energía eléctrica
La electricidad es la consumida por los bancos de resistencias eléctricas. Los bancos de resistencias eléctricas funcionan independientes.
Carga a pintar y soportes a la entrada y salida del horno
La carga está compuesta principalmente por ventanas y puertas de acero Zincado, con espesor de chapa de 0.6mm, la misma está suspendida en percheros de acero. La carga y sus soportes entran al horno a temperatura ambiente; al salir del horno lo hacen a alta temperatura y se deja enfría en el exterior. La determinación de su magnitud se hace a partir de la capacidad calorífica del acero, de la masa y de la temperatura a la que salen del horno. La cantidad de calor que se lleva la carga se calcula por la siguiente ecuación:
(1)
Donde:

Cantidad de calor.

Masa de la carga o soporte.

Calor específico del material de la carga o soporte.

Temperatura de la carga al salir del horno.

Temperatura del ambiente del taller.
Pérdidas de calor a través de las paredes
Para el cálculo de las pérdidas de energía por transferencia de calor en las paredes del horno, se emplea la ecuación de enfriamiento de Newton, con el coeficiente Global de transferencia de calor por convección-radiación
. Determinación de hc: se utilizan las ecuaciones simplificadas que propone Holman, 1998(tabla 1), las cuales son aplicables al aire a presión atmosférica. El primer paso es establecer el criterio de Rayleigh (
), para determinar el régimen.
Con el régimen, tipo y posición de la superficie se escoge la fórmula de hc.
Determinación de hr: se utiliza la ecuación (3). En este caso, el valor de
por lo que el término
se desprecia, quedando de la siguiente forma la ecuación:
(2)
Los valores de
fueron obtenidos en Holman 1998
Cálculo de las pérdidas de calor: se utiliza la ecuación
(3)
Selección del espesor de aislante térmico
Para el recálculo de espesor de aislamiento térmico donde lo requiera se utilizó el software INDUVER versión 1.2 de la firma ISOVER.
Ensayos de calidad del secado de la pintura en polvo
Para llevar a cabo recubrimientos satisfactoriamente, deben adherirse a los productos en los que se aplican. Una variedad de ensayos reconocidos se puede utilizar para determinar qué tan bien un recubrimiento se adhiere al producto. Para efectuar estos ensayos es necesario realizar un análisis del ciclo de polimerización, con el fin de observar el comportamiento de la variación de la temperatura con respecto al tiempo del horno de polimerización durante un ciclo de horneado de 20min, incluyendo los procesos de carga y descarga para observar su comportamiento.
La curva de temperatura contra tiempo que se obtiene demuestra las pérdidas de temperatura en un aproximado de 13ºC. Según la información el horno puede adherir bien la pintura al producto en un rango de temperatura de
a
. Como una de las medidas para reducir el consumo energético se procede a analizar las pinturas que se utilizan en los productos, para este análisis se realizan los ensayos mencionados anteriormente utilizando como variables la temperatura y el tiempo.
Las pinturas utilizadas tienen características propias en cuanto al tiempo y la temperatura que necesitan para la operación de horneado.
Ensayos de calidad del secado de la pintura
Diseño experimental
Para la realización de los experimentos, con vista a correlacionar la calidad del secado con la temperatura y el tiempo de permanencia en el horno (fig. 2), se planteó un diseño experimental multifactorial del tipo de dos factores, el mismo se modeló en el software STATGRAPHICS Plus 5.1, obteniéndose la matriz experimental.
Para cada experimento se realizarán diferentes ensayos sobre la calidad del secado los cuales se exponen a continuación su modo de realización, obteniéndose valores de calidad desde 1 a 5, donde 1 es la mínima y 5 el máximo. Estos resultados se pasarán al software STATGRAPHICS Plus 5.1, con el que procesarán los resultados y se obtiene la dependencia a través del método estadístico de la regresión múltiple.
Ensayo de adherencia
El muestreo se hará según la norma ISO 2409 2007 y ASTM D 2197 de 1996.
Ensayo de Flexibilidad
Este trabajo se sustenta bajo la regulación de la norma ISO 1519.
Ensayo de corrosión
Este ensayo se sustenta bajo la regulación de la norma B117–39T.
Propuesta de instalación de la precámara y poscámara en el horno
Para recuperar el calor de la carga del horno se hace la propuesta de una precámara y poscámara, esta a su vez amortiza la salida del aire caliente del horno y aumenta el tiempo efectivo de permanencia de la pintura a altas.
Las dimensiones de la precámara y la poscámara se propone que sean con las mínimas posibles, las cuales deben permitir alojar el total de la carga, y el funcionamiento del horno, en cuanto a aperturas de puertas y capacidad de la carga del horno; las dimensiones interiores serán aproximadamente de 1780 mm de ancho, 2800 mm de largo y 3180 mm de alto. En las mismas se instalarán dos conductos de conexión entre ellas, con dos ventiladores que ayudarán a la circulación del aire y aisladas térmicamente.
Recuperación del calor en las pre y poscámara.
El proceso de recuperación se realizará de las ventanas y soportes calientes a las frías utilizando como sustancia de trabajo el aire existentes en ambas cámaras, el cual se hará circular de manera forzada por dos ventiladores. Para obtener la temperatura final a la que quedarán las ventanas entrantes se harán las siguientes consideraciones:
- La temperatura en todo el sistema se iguala en el transcurso del tiempo.
- Se asume que las pérdidas de calor por las paredes representan un 5% del calor que portan las ventanas y soportes, como margen de seguridad en los cálculos.
Por lo que la ecuación de cálculo queda de la siguiente forma:
(4)
Donde Q1→ Calor de las ventanas y soportes que salen del horno.
Q2→ Calor del aire de las pre y poscámara.
Q3→ Calor de las ventanas y soportes que entran del horno
Como consideramos que se pierde un 5% del calor a recuperar Q1 lo multiplicamos por 0.95, quedando:
(5)
Desarrollamos la ecuación y obtenemos la ecuación que nos dará la temperatura final de las ventanas y soportes que entran fríos y nos da la medida de la cantidad de calor que se recupera:
(6)
Donde:
→ masa de las ventanas y soportes.
→ masa del aire.
→ calor específico del acero.
→ calor específico del aire.
→ Temperatura de las ventanas y soportes a la salida del horno.
→ Temperatura del aire al inicio del proceso.
→ Temperatura de las ventanas y soportes a la entrada del horno.
Resultados y Discusión
Balance energético del horno
Los resultados de los cálculos del balance energético del horno se exponen a continuación, El consumo y pérdidas del horno quedan regido por los siguientes elementos:
(7)
→ Calor perdido por las paredes.
→ Calor que absorben las ventanas, los soportes y el aire interior del horno.
→ Energía eléctrica consumida por los ventiladores del horno.
En una horneada, la cual dura 20 minutos, se pierden 23647,7kJ, que equivalen 6,56kWh, representando el 52% del consumo de la energía suministrada en este tiempo. De estas pérdidas, el mayor por ciento (54%) está en el techo del horno y los dos ventiladores, 3,55kWh. El techo está mal aislado y los dos ventiladores no están aislados térmicamente.
La carga del horno está compuesta por 10 ventanas y sus soportes, la misma sale a altas temperaturas.
En el horno, en cada horneada, se emplea 6,15kWh en calentar la carga; lo que representa el 43,9% de la energía suministrada, de ella 1.125kWh en los soportes de las ventanas que no son carga útil. El aire absorbe 1,32kWh, lo que representa el 10% de la energía suministrada. Por los criterios expuestos, se observan dos problemas fundamentales en el horno: uno es las excesivas pérdidas de calor en algunas partes mal o no aisladas térmicamente; y el otro es gasto innecesario de calor empleado en calentar los soportes de acero de las ventanas, donde se emplea un gran por ciento de la energía suministrada al horno.
Las mediciones de consumo del horno arrojan un consumo de 14,3kWh por horneada. En los cálculos realizados sumando las pérdidas, la ganancia de energía de la carga y el consumo de los dos motores de los ventiladores se obtiene un total de 14kWh; la diferencia entre las energías entrantes y salientes del horno es de 0,3kWh, lo que significa un 2.09% de error, siendo aceptable el balance total de energía.
La eficiencia energética para este sistema sería de la siguiente forma:
(8)
Donde:
Ep
es la energía de los productos en este caso energía absorbida por las ventanas.
Eelec
energía eléctrica consumida por el horno en sus resistencias y motores de los ventiladores.
Según esta ecuación y con los datos obtenidos arroja el siguiente valor de eficiencia:

Ensayos de calidad del secado de la pintura
El análisis de Regresión Múltiple, realizado en el software STATGRAPHICS Plus 5.1, con los valores de calidad obtenidos de los ensayos, arrojó como resultados:
- R-cuadrado = 80,235: porcentaje de la relación existente entre las variables independientes y la variable dependiente.
- Los resultados del ajuste a un modelo de regresión lineal múltiple que describen la relación entre Calidad y las variables independientes (temperatura y tiempo) como se muestra en la fig.3.1. La ecuación del modelo ajustado es:
Donde: C
Calidad, T
temperatura, t
tiempo
A partir del uso de la ecuación que modela la dependencia de la temperatura y el tiempo con respecto a la calidad esperada, se propone variar los parámetros de permanencia de los productos en el horno con una norma de trabajo de 15minutos y 210°C, en caso de realizar las mejoras de diseño del horno.
Propuestas de mejoras para el horno de secado de pintura
En el horno se proponen dos tipos de medidas para sus mejoras: una del tipo de diseño y la otra del tipo organizativa o de cambio en el flujo productivo.
Mejoras en el diseño del horno
Mejoras en el aislamiento térmico
La primera propuesta de reforma del diseño del horno es mejorar el aislamiento térmico, con el objetivo de llevar la temperatura superficial del horno a 45°C. Al llevar la temperatura superficial del horno, a ese rango, al total de las superficies del horno, se lograría disminuir de 6,88kWh de pérdidas de energía por horneada de 20minutos a 1,04kWh, lo que equivale a reducir, en poco más de 6 veces, las pérdidas por este sentido.
El espesor que se necesita para aislar térmicamente las áreas mencionadas es de 16cm (común para todas las áreas). Según el catálogo (Bricomarkt 2010) de las ofertas, se propone el material lana de vidrio (roca) con espesor de 8cm (se requiere el doble del material); sus dimensiones y precios se muestran a continuación:
Cálculo del ahorro de energía eléctrica
El ahorro de energía eléctrica en nuestro caso está dado por tres líneas fundamentales:
- Mejoras en el aislamiento del horno.
- Bajar la temperatura y tiempo de trabajo del horno.
- Recuperación del calor de los productos.
Los tres casos por los que se ahorra energía no pueden verse por separado puesto que las tres están interrelacionadas, depender todas de la temperatura interior del horno y del tiempo de permanencia en este.
Los cálculos de recuperación del calor arrojaron una ganancia de 1,94kWh, que representa energía que se deja de consumir en el interior del horno.
Actualmente se pierden 6,88kWh por horneada de 20minutos, si se realizan las mejoras del aislamiento térmico, se baja el ciclo de horneado a 15 minutos, la temperatura del interior del horno a 210°C, las pérdidas por transferencia de calor en sus paredes sería de 1,06kWh.
Sumando los nuevos valores más los dos nuevos ventiladores a instalar el nuevo consumo quedaría:
(9)
→ Donde los 1.94kWh son los que se dejan de consumir por la recuperación del calor.

Para el nuevo consumo calculamos la eficiencia energética del horno:
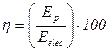
(10)
Con estas mejoras se elevaría la eficiencia térmica del horno de un
26,3% actual a un
51%.
Resultados Obtenidos
Con todas estas mejoras la eficiencia del horno se elevaría hasta un 51% ahorrando 1514.9 kWh al año con los niveles actuales de producción y aumentando la productividad del horno en un 25%. Al introducir estos cambios la productividad del horno aumenta en un 25%, de 195 ventanas por día ahora pasa a 260, disminuyendo el kWh/ventana de 1.405 a 0.725.
Evaluación Económica.
La recuperación de la inversión se logrará con el ahorro de energía eléctrica resultante de las medidas propuestas de mejoras del horno.
El promedio de producción de ventanas/año en los últimos tres años fue de 23796, de mantenerse este nivel productivo el ahorro sería del orden de los 15149 kWh. El precio del kWh es de 0.10$/kWh, el cual arrojaría un ahorro por dejar de consumir energía de 1514.9$/año.
Aplicando la metodología del análisis financiero expuesta en el capítulo I, se obtienen los siguientes resultados:
El VAN es mayor que cero, el TIR mayor que la tasa de actualización al quinto año de ejecutar el proyecto se recupera la inversión. Aunque les bueno señalar que la productividad del horno aumenta en un 25%. Los cálculos se realizan con los actuales niveles de producción que son 118 días al año. Con la planta funcionando a plena capacidad e introduciendo las mejoras propuestas el análisis fuera entonces el siguiente:
Si la planta funcionara a plena capacidad la inversión se recuperaría en tres años.
CONCLUSIONES
- En el horno se pierden 6,56kWh en transferencia de calor a través de sus paredes, representando el 46.7 % de la energía suministrada, y localizándose sus principales focos en las áreas del techo y los ventiladores. La carga absorbe 4,83kWh, que constituye el 34.59% de la energía suministrada, de ella 1,125kWh es en los soportes, los cuales son carga no útil.
- A partir de la ecuación obtenida se realiza la propuesta de disminuir el tiempo de permanencia a 15minutos y bajar la temperatura de operación de 220ºC a 210ºC, si se ejecutan las mejoras al diseño del horno.
- Con la mejora del aislamiento térmico, disminución de la temperatura y tiempo de duración del ciclo de horneado e instalación de una pre y poscámara con el propósito de recuperar el calor de las ventanas y soportes al salir del horno el consumo de este bajaría de 14,05kWh a 7,26kWh y la su eficiencia mejoraría de un 26,3% a un 51%.
- Teniendo en cuenta el ahorro de 15149kWh/año que provocarían las mejoras, la inversión se recupera al quinto año de ejecutar el proyecto, si trabajara a plena capacidad la inversión se recuperaría en su tercer año. Todo esto con una productividad aumentada en un 25%.
BIBLIOGRAFÍA
- Alegría Felices, F. e. a. (1982). Técnicas de Conservación Energética en la Industria. La Habana, Ediciones Revolucionarias.
- ASTM (1997). Standard Practice for Operating Salt Spray (Fog) Apparatus1, ASTM. B 117 – 39 T: 8.
- Bricomarkt (2010) Tarifas de Precio Lana de Roca. Volumen, 60 DOI:
- Construmatica (2008) Pintura en polvo. Volumen, DOI:
- Consumer (2002) Pintura y decoración. Volumen, DOI:
- Defelsko (2010) Adhesion Testing Methods. Volume, DOI:
- Defelsko.com (2010) Adhesion Testing Methods. Volume, DOI:
- Domínguez, J. A. y. e. a. (1987). Introducción a la corrosión y protección de metales. La Habana, Cuba, ENPES.
- Holman, J. P. (1998). Transferencia de calor. Madrid, España, McGraw-Hill/Interamericana de España, S.A.
- ISO (2007). Paints and varnishes, cross-cut test. ISO 2409: 2007.
- ISO (2009). ISO 9001. Vocabulario.
- ISO (2010). Paints and varnishes -- Bend test (cylindrical mandrel). ISO 1519.
- Kern, D. Q. (1979). Procesos de transferencia de calor. Ciudad de La Habana, Cuba, Pueblo y Educación.
- López Planes, R. (1988). Diseño estadístico de experimentos. La Habana, Cuba, Científico-Técnico.
- McCabe, W. L. J. C. S. (1985). Operaciones Básicas de la Industria Química, Ediciones Revolucionarias.
- Miller, I., John E. Freund, Richard Johnson (2007). Probabilidades y Estadísticas para Ingenieros. La Habana, Editorial Félix Varela.
- Molina Igartua, L. A. (1993). Manual de eficiencia térmica en la industria. Bilbao, España, CADEM.
- Moran M.J, H. N. S. (2000). Fundamentos de termodinámica Técnica, REVERTRE S.A.
- Novelispainted (2007) Pintado del aluminio, clave de las ventajas. Volumen, DOI:
- Ochoa George, P. A. (2008). Las Producciones más Limpias en la Gestión Empresarial. La Habana, Cuba, Félix Varela.
- Pávlov, K. F. R., P. G. y Noskov, A. A. (1981). Problemas y ejemplos para el curso de operaciones básicas y aparatos en tecnologías químicas. Moscú, URSS, MIR.
- Sociales, M. d. T. y. A. (2008). Guía Técnica sobre condiciones ambientales en los lugares de trabajo, INSHT, España.
- Turrini, E. (2006). Por el Camino del Sol. La Habana, Cuba, CUBASOLAR.
Fecha de recepción: 08 de mayo de 2013
Fecha de aceptación: 01 de enero de 2015